Insulation effectiveness is compromised by thermal bridging – this is where heat escapes through materials which conduct heat more easily. Timber is one of those materials. Timber framing has a significantly lower R-value than the bulk insulation materials typically used in walls of new houses. As framing content increases, wall R-value, as a whole, decreases accordingly.
The Building Research Levy funded a multi-stage project to explore the extent of the problem and possible solutions.
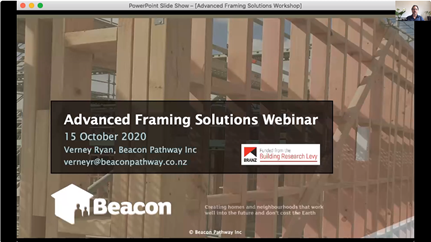
Over 80 industry stakeholders participated in a webinar to discuss and collaborate on potential solutions for better insulated walls. We hope this will be an ongoing collaboration to find practical cost-effective and better performing solutions so the video of the entire webinar is available here.
Stage One: Measuring the extent of timber framing in external walls
What we did
Stage One of the Wall Project measured the percentage of timber framing in external walls in 47 new builds in Auckland, Christchurch, Wellington and Hamilton.
Frame and Truss manufacturers supply in excess of 90% of the framing to new residential builds in New Zealand. The research approach utilised hard copies of F&T panel elevations and plan layouts on site to assist with data gathering. The team also undertook a series of interviews with major suppliers to industry, cladding and Frame and Trust manufacturers, which proved crucial to understanding how the design process worked and what drove design decisions.
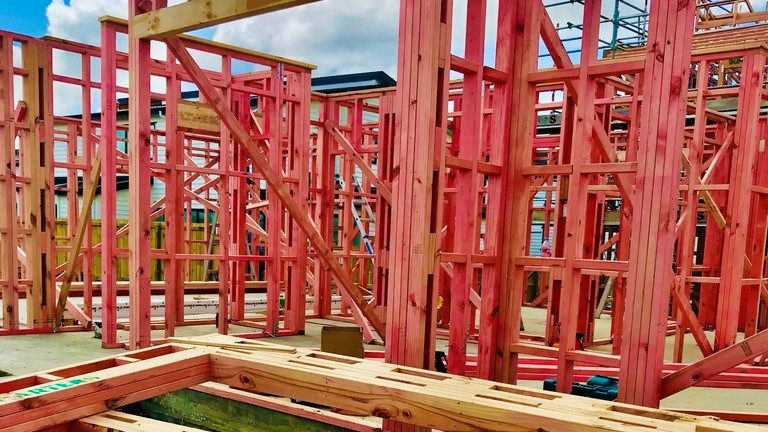
Our findings
The results show that the average percentage of timber framing compared to the area of the wall is above 34%. This is much higher than the 14 – 18% framing content generally assumed by both regulators and the industry when undertaking compliance calculations.
As more timber framing in the wall means more limited space for insulation, this suggests that the overall thermal performance of the walls is lower than calculated.
Little additional framing was added on site – the average additional site-added, full-depth framing is just 0.7%. Builders and subtrades are not responsible for adding unnecessary framing.
Rather, the research highlighted evidence that increasing framing content is being driven by the requirements of various regulations, mostly in relation to structure and weathertightness (including cladding requirements).
Read the full report here:
Stage Two: Exploring drivers for high timber content
What we did
Working with an experienced frame and truss detailer and using a simple standard house design, the team analysed whether current detailing techniques were adding any unnecessary timber.
They then explored how much timber content could be reduced within current standards, regulations, specifications, cladding types and construction techniques.
Our findings
The analysis suggests that there is little ‘unnecessary’ timber being added to framing. Each piece of 90mm x 45mm timber is added to the frame for regulatory and practical reasons – structure, weathertightness, and fixings for cladding, linings and additional fittings.
Even with a relatively simple house design, the framing content could not be reduced to a level below a 25% percentage of framing.
Stage Two: The impact of high timber content
What we did
Five sample houses (all complying with the NZ Building Code) were modelled to quantify
- the as-built wall R-values
- the impact of the weak points on R-values
- the R-values of a reduced framing content of 25%.
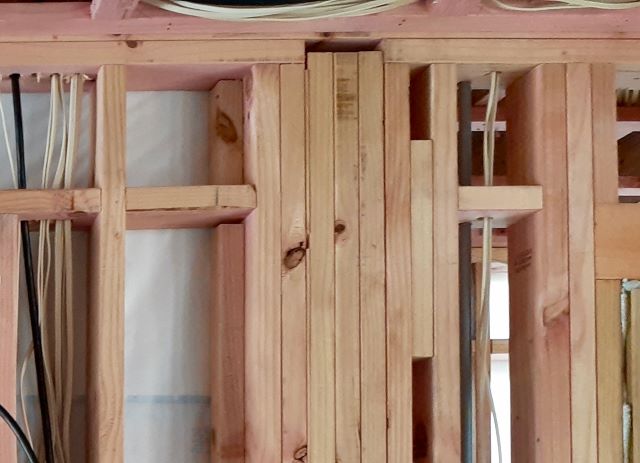
Our findings
The results showed the overall thermal resistance of external walls (as-built via modelling) varies between R1.2 – R1.4, even with R2.8 insulation installed. This is well below the recommended R1.9/R2.0 set out in NZ Building Code Clause H1 and also below the required minimum of R1.5 set out in Building Code Clause E3.
Upgrading the five typical weak points together produces small increase in wall construction R-values, while limiting the percentage of wall framing to 25% would only result in an overall wall R-value increase of 6% for R2.0 insulation and 8% with R2.8 insulation.
However, the largest single increase in wall construction R-value is attributed insulating the floor slab edge on single level houses which improves the whole house wall construction R-value by around 40%.
Stage Two: Alternative wall solutions
Industry workshop
This workshop focused on exploring pragmatic and buildable framing solutions for New Zealand which result in a radical improvement to the thermal envelope.
The workshop featured sessions on:
- Current wall performance: Preliminary results from modelling of case study houses (Guy Penny, Beacon Pathway)
- The Zero Energy House (Jo Woods & Shay Brazier, Re/volve Energy)
- Alternative wall systems (Glenn Murdoch, Theca Architecture)
- Thermally improved construction details (Jason Quinn, Passive House Institute NZ)
- Current exemplars and the Superhome approach (Bob Burnett, Damien McGill, Dan Saunders – Superhome Movement)
- Medium density housing framing solutions (Shawn McIsaac, Oculus Architectural Engineering)
Watch the webinar
Regulatory change needed
The research highlights a sizable performance gap between the R-values intended by NZ Building Code H1/AS1 (R1.9/R2.0) and actual whole wall construction R-values. Apart from poor energy efficiency, walls with construction R-values below R1.5 are much more likely to develop condensation and mould. In simple terms, our walls are not as effective at keeping us warm, nor as healthy, as we might have assumed.
One reason for this may be that NZS 4218 and NZ Building Code Clause H1/AS1 use a definition of a wall that excludes corner studs, extra partition wall studs and framing around windows, called ‘clear wall’ or ‘typical wall’. This is a section of wall that has the lowest timber-framing-to-insulation ratio and will therefore, have a higher R-value than the rest of the wall.
In reality, however, most walls and wall panels are made up of a complex arrangement of studs, nogging, openings and supporting structures, all of which add to heat loss through thermal bridging and should be accounted for when calculating the thermal performance of our buildings. We suggest that using a ‘whole wall’ definition to calculate R-value, NZS 4218 and NZ Building Code Clause H1/AS1 will more accurately represent the levels of thermal bridging in standard NZ construction of 90mm timber-framed walls.
Download the Stage Two report:
Watch the Thermal Bridging in Timber-framed Walls webinar which summarises the entire research for regulators, designers and builders. This can be streamed from the BRANZ website.
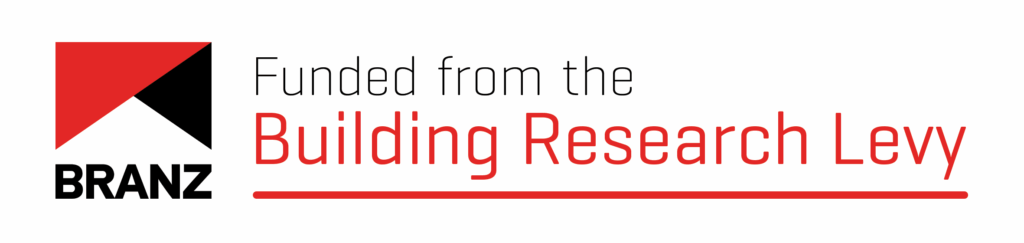